Molly Bagby is an employee at Highland Woodworking who is taking the 2 Week Basic Woodworking course at Center for Furniture Furniture Craftsmanship. Although she grew up at Highland Woodworking from a mere 1 week old, her knowledge of woodworking skills is limited. With this class, she intends to change that. You can follow her on Instagram @HighlandWoodwoman.
Since this is a 2 week class, the school sets up housing hosts for those who come in from out of town. I arrived in Hope, Maine around 10:30pm the day before my class started after a brief detour visiting my sister Kelley, a fellow author on this blog. I was easily able to find the house and my room, and my host was gracious enough to leave handwritten notes everywhere to tell me where everything was located. The next morning, she was in the kitchen when I came downstairs and she and I chatted a bit. Her name is Deb and she is active in the local arts community.
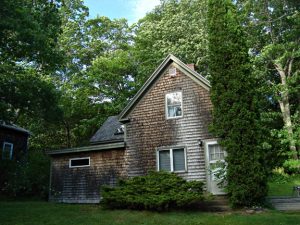
My residence for the 2 weeks I’m studying at Center for Furniture Craftsmanship
After a quick stop for some breakfast at The Market Basket (a deli I’ve frequented many times on my visits to the Lie-Nielsen Toolworks factory) it was off to my first day of woodworking school.
Each 2 week class at Center for Furniture Craftsmanship (CFC) accommodates 12 people (i.e there are 12 workbenches plus 1 for the instructor). When I entered the Workshop Building (1 of 5 buildings on campus), all but 2 of the workbenches were occupied with students ready and raring to go! I found an empty workbench at the back of the room and 5 minutes later, a guy named Mike Z from NYC showed up and took the last bench (and became my bench mate since our benches were butted up next to each other, as every 2 benches were situated in the classroom). Mike has been a really cool guy to get to know and we both have several things in common (being the 2 youngest people in the class and both having lived in NYC, among other things).
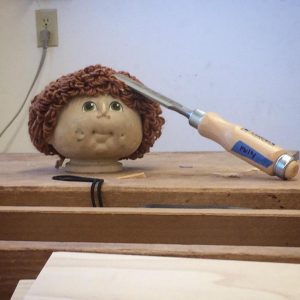
Mike brought this doll head from his school workshop in NYC. It stares at me a lot, so one day I tried to stick a chisel in its head so it would stop staring at me. My chisel wasn’t sharp enough.
Class started promptly at 9am when Peter Korn walked into the classroom and called everyone over to his workbench. He gave a brief overview of the school and then explained what would be happening over the next 2 weeks. He introduced us to Mary Ellen Hitt, the co-instructor for the class, and Eddie Orellana, who has the all-encompassing role of Shop Assistant. Then everyone taking the class introduced themselves. After I introduced myself, Peter noted that Highland Woodworking had donated many of the workbenches found throughout the school.
After introductions, Peter told us one of the most important things to know in woodworking safety: “Oily rags will spontaneously combust.” We haven’t even had our finishing talk yet, but already, this phrase has been repeated multiple times.
The rest of the morning included a basic overview of wood: “We’re going to start with wood…wood comes from trees…” This discussion included types of wood, types of grain, wood thickness, and wood grades. Next, he went right into discussing steel and chisels, which quickly led to the most important aspect of woodworking, sharpening.
I have quickly learned why sharpening is many woodworkers least favorite parts of the trade, but at the same time, I have also learned how important it is to have a sharp tool at hand. Peter went through a detailed step-by-step demonstration of his preferred sharpening process, which I will go into further detail about in an upcoming blog entry dedicated to sharpening and how much I hate love it. For now I will just say that Peter makes everything look really easy.
The last part of the day was spent touring the Machine Room and learning what each machine was used for, as well as safety measures for each machine. While I’ve grown up around power tools and machinery, I’ve never actually used any of it. I am excited to learn, but I am happy that the school likes to focus more on hand tool usage…
The Machine Room consists of the following: a 10″ SawStop tablesaw, a 12″ sliding tablesaw, 8″ and 12″ jointers, 12″ and 15″ thickness planers, 14″ and 20″ bandsaws, drill presses, a lathe, a shaper, a chopsaw, a scrollsaw, a slot mortiser, grinders, a stationary disc/belt sander, and an oscillating spindle sander. There is also full dust-collection.
Every workday ends at 4:30pm with a class meeting to go over the next day’s schedule and then it’s time for shop and workstation clean-up. Peter made sure to note that according to OSHA standards, it is “illegal” to sweep a woodshop. Vacuuming it is!
Read the next blog in this series, The Importance of Sharpening
Follow me on Instagram @highlandwoodwoman to see more photos from the class!