I’m building a pencil post bed for our master bedroom. The four posts, cut from curly maple, were chamfered to a tapered octagonal shape, first on the table saw and then with a 45° chamfer bit using a jig that allowed me to use a handheld router. The router created a nice rounded transition at the point where the chamfers meet the square bottoms of the posts. That would have looked fine as it was, but I decided to add a traditional bit of decorative detail in the form of lamb’s tongues. Lamb’s tongues are, in effect, stops at the end of a chamfer, followed by an ogee shape.

Completed lamb’s tongues
My bed posts are 2-3/4 X 2-3/4″ at the bottom, tapering to 1-1/2″ wide at the top. At the transition point, the chamfers are 7/8″ wide.
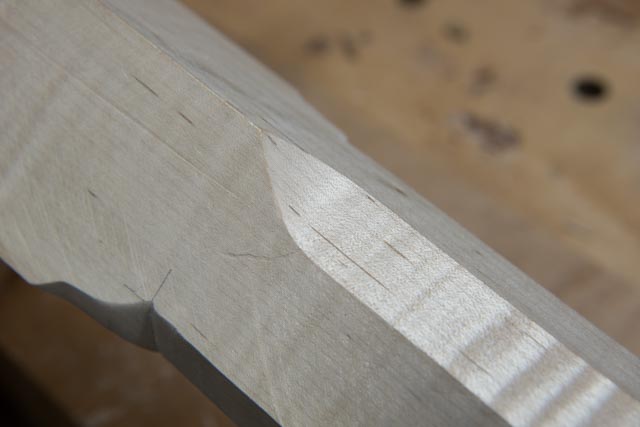
The transition left by the chamfer bit
I made a wooden template in the shape of an ogee based on 7/8″ intersecting arcs.
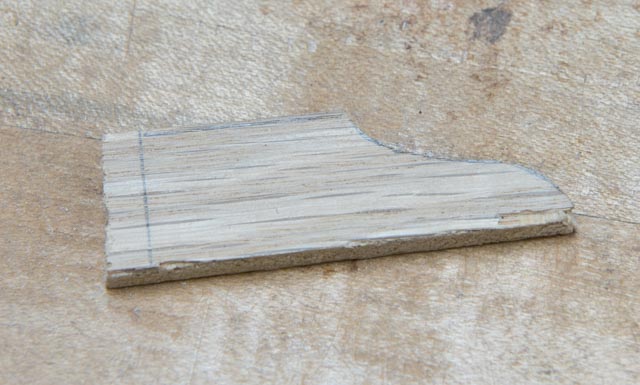
The template
I drew lines marking the location of the stops at the end of the transitions and the baselines that extended out from the edge of the chamfers, then marked the shape of the lamb’s tongue on both sides of the leg.
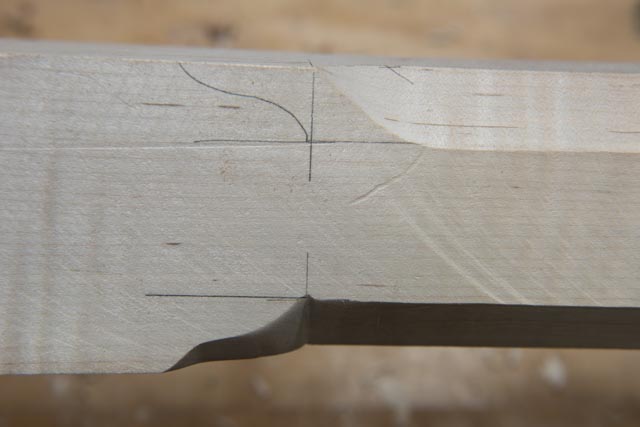
Marked up leg ready to cut
I found that some adaptation was needed from one chamfer to another, since the width of the chamfers sometimes varied slightly.
Once marked, I made a vertical saw cut at the stop line with a Veritas 14 ppi crosscut saw, being careful not to overcut the baselines. Then, using a Shenandoah Tool Works 1 lb. mallet and a sharp 3/4″ bench chisel, I cut away the waste between the chamfer and the stop with the chisel bevel down.
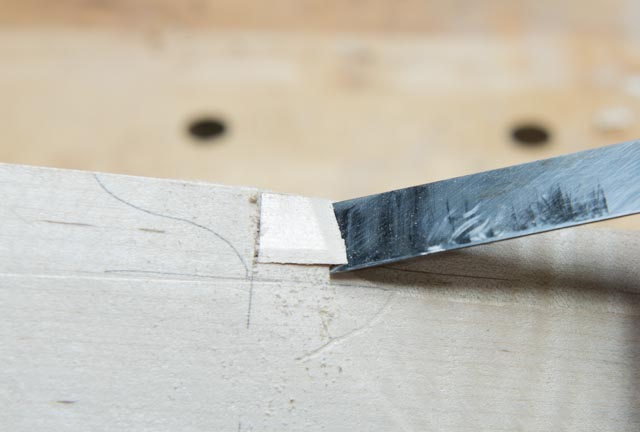
Chopping the waste from the chamfer
I smoothed the chamfer up to the stop with the chisel held flat and bevel up and followed this with a Lie-Nielsen chisel plane and a card scraper to finish the surface. The goal is to get a sharply-defined stop at the edge of the ogee.
I then cut the ogees carefully by wasting away most of the wood with the mallet and chisel, again being careful not to overcut the line.
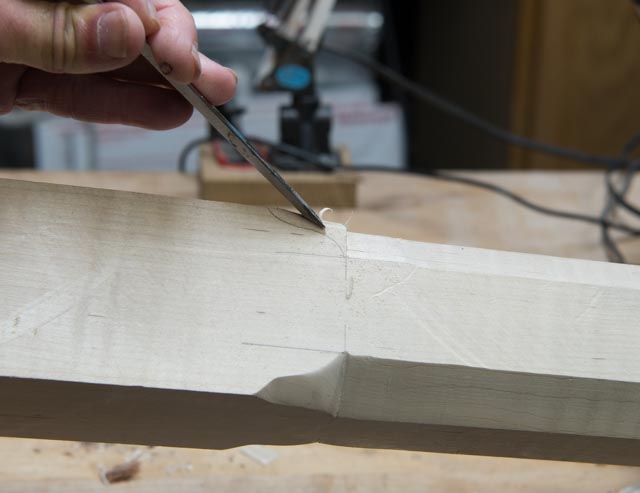
Chopping the waste from the lamb’s tongue
I followed this with a #9 and #13 Auriou rasp, then sanded the surface to 180 grit to eliminate any marks from the rasps. The result: a nice traditional detail to dress up my bed posts.
Norm Reid is a woodworker, writer, and woodworking instructor living in the Blue Ridge Mountains with his wife, a woodshop full of power and hand tools and four cats who think they are cabinetmaker’s assistants. He is the author of the forthcoming book Choosing and Using Handplanes. He can be contacted at nreid@fcc.net.