No Southern-fried Southern boy wants to be called a Yankee, but we share the characteristics of shrewdness and thrift. Thus, each month we include a money-saving tip. It’s OK if you call me “cheap.”
Back in the day, can openers created a sharp-edged disk of metal that was at least as dangerous as a Ninja star.
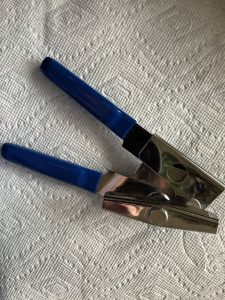
Old School can opener.
There is no telling how many people have been stitched up from handling those. Today, modern can openers cut the lids in such a way that there are no sharp edges.
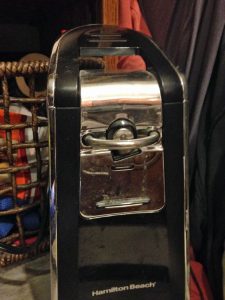
New School can opener.
But, there is yet another benefit. The flat, safe surface is perfect for mixing epoxy. It is dished just enough to make a little depression to contain the epoxy, and you can mix it with a little stick. Just be sure to wash and dry it well before using it.
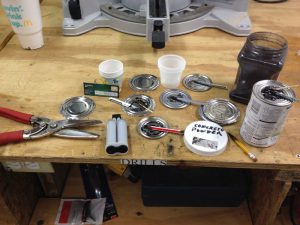
I store epoxy and clean can lids together, along with some old credit cards to cut up for disposable, recyclable stirring sticks and cups for mixing liquid epoxy. Tin snips cut the cards cleanly, and you can make wide or narrow stirrers, according to your needs. In addition to TransTint, I have used concrete coloring powder to color epoxy. Solids accelerate curing.
Jim Randolph is a veterinarian in Long Beach, Mississippi. His earlier careers as lawn mower, dairy farmer, automobile mechanic, microwave communications electronics instructor and journeyman carpenter all influence his approach to woodworking. His favorite projects are furniture built for his wife, Brenda, and for their children and grandchildren. His and Brenda’s home, nicknamed Sticks-In-The-Mud, is built on pilings (sticks) near the wetlands (mud) on a bayou off Jourdan River. His shop is in the lower level of their home.Questions and comments on woodworking may be written below in the comments section. Questions about pet care should be directed to his blog on pet care, www.MyPetsDoctor.com. We regret that, because of high volume, not all inquiries can be answered personally.